Features of stone milling on CNC machines. Models.
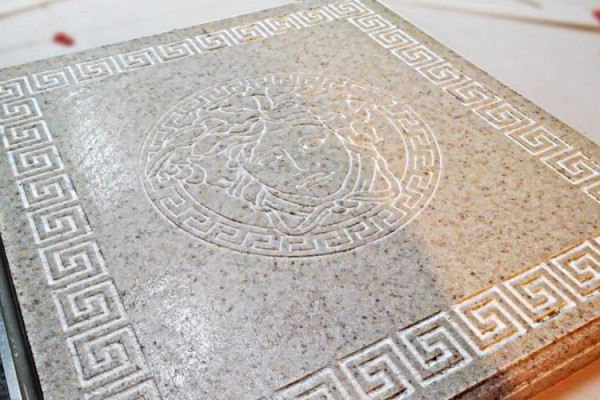
In this article we will talk about the features of working with stone, advantages and disadvantages, specifics, and general recommendations.
You can create beautiful and stylish stone products on CNC machines using the data listed below and our 3D models presented on the website.
About stone as a material:
Since ancient times, stone has been valued for its durability, moisture resistance, accessibility, and visual appeal.
Stone products retain their properties for centuries, look expensive and good.
Stone has always been widely used in sculpture, architecture, construction, and in the creation of household and decorative items.
Today, a wide variety of products are created from it: statues and bas-reliefs, decor, facing materials, engravings, tabletops and much more.
Stone milling:
There are many ways to process stone, but milling has many advantages over other options. It allows you to obtain high-quality results, with high accuracy, in the shortest possible time. It helps to produce complex relief and decoration on stone, to obtain both standard and non-standard products designed specifically for the customer, and copes well with any type of stone. Can be controlled remotely, eliminating the need to breathe dust. It is quite simple, does not require long training, allows you to automate processes and get rid of manual labor.
Types of stone by hardness:
There are different stones, depending on the hardness scale.
- Soft - shell rock, limestone, gypsum. Such stones can be processed with any cutters, even those suitable for working on wood and plastic. The main thing here is that the cutting part of the tool is as sharp as possible. Cutting fluids are used.
- Medium - for example, marble, calcite, dolomite. When processing these stones, diamond cutters or polycrystalline engravers are required.
- Hard and extra hard stones include opal, quartz, borders, etc. In this case, both cutters and machines must be of increased strength. These can be polycrystalline conical engravers, diamond cutters. Coolant must be used to avoid overheating.
Difficulties in working with stone:
- The key difficulty in creating stone carvings is its fragility combined with its hardness. This makes figure cutting a complex, almost virtuoso task. After all, the slightest awkward movement can ruin the stone blank.
- In addition, the high hardness of the stone leads to the risk of tool breakage. To mill stone, special cutters are required, which are carbide or diamond-coated cutters, which are characterized by increased hardness.
- Another disadvantage when working with stone is its enormous weight. That is, the work table of the milling machine must be strong enough, suitable for workpieces of this weight. The coating on it must be resistant to abrasion and indentation. A protective coating is often used for this purpose.
- It is important that the cutter is securely fastened (taking into account the force with which the cutting tool acts on the material).
- It is advisable to avoid defects, since stone is quite expensive, so each pass through the material is not done as a pass, but for the final product and the finished result. It is important to correctly specify processing modes
- If the product is large enough, it will take quite a long time to make it.
- At the same time, milling is significantly complicated by the formation of large amounts of crumbs and dust. This makes working with the material difficult and unsafe. Additionally, this imposes its own requirements on the type of room. For equipment for the machine. For example, it is believed that excessive dust can lead to computer failure.
- The machines themselves for processing stone usually cost significantly more, since they have all the necessary qualities (equipped with a more powerful spindle, a larger and stronger working field, and additional equipment). Carbide cutters can also cost more. Thus, the production of stone products is more expensive than wood.
Recommendations:
There are certain recommendations when working with hard stone blanks.
Let's talk about some of them:
- For roughing on stone, end mills with a diameter of approximately 6 mm are used, to a depth of no more than 1 mm per pass.
- It is recommended to cut the tool into the surface of the workpiece at an inclined angle (in roughing mode).
- Finish milling is performed with a cutter with a diameter of 6 mm and a conical shape. The step in this case is 01.-0.3 mm (for rough work - approximately 2 mm).
- The use of diamond cutters in comparison with carbide cutters allows one to slightly increase the processing speed (averaging 20-30 mm/s when working with stone).
- If the machine vibrates strongly, this can reduce the quality of processing and lead to the formation of chips. However, most modern machines have sufficient rigidity. In addition, vibrations can be avoided if you take care to securely secure the workpiece on the work table.
Key requirements when working with stone of any strength level:
- Pick up suitable tools
- Ensure the supply of cutting fluid
- Avoid high spindle speed
- Try to connect a laptop or tablet to the CNC that can be taken out of the room, since in the room where stone is milled there is often a high level of humidity and dust rises.
- It is advisable to choose a machine that can handle stones of any hardness and is capable of performing different types of work.
Models:
To work with stone on CNC machines you need high-quality 3D models. You can buy these on our website. We offer a wide range of ready-made models for creating a wide variety of products. In addition, you can order the development of a model if the option you need is not on the website.
Call, write. Ask questions!
Other articles you may be interested in:
Milling and processing of foam plastic and expanded polystyrene on CNC machines. 3d models
Decorative fountains on CNC machines. Models of sculptures.
Art objects on CNC: 3D models
Sculptures in landscape design. CNC manufacturing. 3D models.